تستهای مواد (بخش دوم)
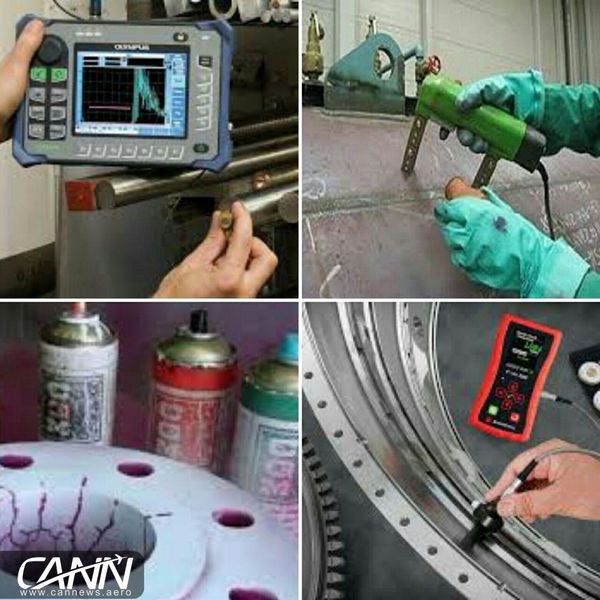
همانطور که در بخش اول گفته شد بطور کلی تستهای مواد به دو بخش مخرب و غیر مخرب تقسیم میشوند و در مقاله اول به بررسی تستهای مخرب پرداختیم، در این مقاله اما به بررسی تستهای غیر مخرب خواهیم پرداخت.
همانطور که در بخش اول گفته شد بطور کلی تستهای مواد به دو بخش مخرب و غیر مخرب تقسیم میشوند و در مقاله اول به بررسی تستهای مخرب پرداختیم، در این مقاله اما به بررسی تستهای غیر مخرب خواهیم پرداخت.
- تستهای غیر مخرب : (Non-destructive tests NDT)
این نوع تستها بطوری انجام میشوند که بعد از انجام تست امکان استفاده مجدد از قطعه وجود داشته باشد به عبارت دیگر تستهای غیر مخرب عبارتند از ارزیابی مواد و قطعات بدون اثر گذاشتن بر کارایی آنها، پس میتوان از این نوع تستها در فرایند تعمیر و نگهداری استفاده شود، اکثر شرکتهای هواپیمایی دارای واحد مهندسی-تعمیرات نمونهای هرچند کوچک از کارگاه تست غیرمخرب یا NDT را در آشیانههای خود دارند.
انواع تستهای غیرمخرب:
- تست چشمی Visual Testing:
این تست یک فرایند تست اولیه است و در برخی موارد فقط همین تست انجام میشود، میتوان گفت که 80% تستها به تست چشمی ختم میشود. این تست معمولا توسط یک بازرس چشمی که هم دارای دانش تست و هم تجربه آن است انجام میشود.
در تست چشمی دو نوع ابزار استفاده میشود که نوع اول ابزارهای ساده مثل ذرهبین، چراغقوه، کولیس، آینه و ... است و نوع دوم ابزارهای پیشرفته است که در هر فرایندی متفاوت است مثلا بازرس فنی هواپیما از یک سری ابزارات پیچیده استفاده میکند و بازرس جوشکاری از ابزارآلات دیگری استفاده میکند.
یکی از ابزارآلات پیشرفته مشترک در تست چشمی borescope ها هستند که برای بازرسی قسمتها یا سقوح داخلی بکار برده میشوند، از اصلیترین قسمتهایی که در فرایند تعمیر و نگهداری از borescope استفاده میشود در بازرسی موتور جت مخصوصا در قسمت تیغههای کمپرسورها و توربینها میباشد، borescope ها دارای دو نوع انعطاف پذیر و ثابت هستند که بسته به محل مورد استفاده از آنها استفاده میشود.
- بازرسی با مایعات نافذ :Liquid Dry Penetrants Tests
از این روش به منظور شناسایی عیبهای سطحی استفاده میشود، این روش به تست چشمی کمک میکند که عیبهای بسیار ریز شناسایی شوند، به عبارت دیگر عیبهایی همانند ترکها و حفرات بسیار کوچک در بازرسی چشمی به علت کم بودن قدرت تفکیک چشم انسان قابل شناسایی نیستند بنابراین بازرسی با مایعات نافذ به منظور شناسایی این دسته از عیبها بکاربرده میشود.
تست مایعات نافذ میتواند با مایعات قرمز رنگ (که عیب توسط ماده آشکارساز پدیدار میشود) و یا مایعات فلوئورسنت (که عیب به واسطه نور فرا بنفش آشکار میشود) انجام شود باید در نظر داشت که این مایعات اغلب مایعات نفتی بوده و با آب قابل شست و شو میباشند.
در این روش ابتدا قطعه تمیز میشود سپس مایع نافذ از طریق غوطهور کردن قطعه در آن یا اسپری کردن به قطعه افزوده میشود سپس بعد از اندکی تامل (برای نفوذ کامل مایع در شکافها) ماده اضافی از سطح قطعه پاک میشود، پس از این مرحله قطعه با استفاده از پودر آشکار ساز یا نور فرا بنفش مورد بازرسی قرار میگیرد.
- بازرسی با ذرات مغناطیس Magnetic Particle Inspection:
در این تست از یک پودر مغناطیس یا یک سیال مغناطیس به همراه یک میدان مغناطیسی شدید برای شناسایی عیبها استفاده میشود، با این روش میتواند عیبهای سطحی و عیبهای نزدیک به سطح را شناسایی کرد.
در این روش ابتدا قطعه تمیز شده و در صورت نیاز مغناطیس زدایی میشود سپس توسط جریان الکتریکی یا یک آهنربای دائمی خطوط شار مغناطیسی درون قطعه ایجاد میشود، این خطوط درون قطعه از قطب جنوب به قطب شمال امتداد دارد در صورتی که درون قطعه یک عیب سطحی یا زیرسطحی همانند ترک وجود داشته باشد خطوط میدان در محل عیب دچار تغییر شکل میشود و از قطعه بیرون میزند که به آنها اصطلاحا نشتی میدان یا نشتی شار مغناطیسی گفته میشود، در چنین شرایطی یک پودر مغناطیسی یا یک سیال مغناطیسی بر روی سطوح قطعه پاشیده ممیشود و به علت وجود نشتی میدان مغناطیسی در محل عیب، ذرات مغناطیسی در محل عیب تجمع پیدا میکنند بنابراین نشانهای از بوجود میآید.
در صورتی که خطوط میدان بر امتداد عیبها عمود باشد، شناسایی عیبها به راحتی صورت میگیرد و اگر خطوط میدان و امتداد عیبها موازی باشند عیبها قابل شناسایی نیستند، در تست با ذرات مغناطیس نیاز است که تست در دو جهت عمود بر هم صورت گیرد.
- تست پرتونگاریRadiographic Tests:
در پرتونگاری از پرتوهای X و گاما استفاده میشود که از امواج الکترومغناطیس بوده و طول موج بسیار کوتاه و فرکانس و انرژی بسیار بالایی دارند، در این روش پرتوها از قطعه مورد آزمایش عبور کرده و بر روی یک فیلم مخصوص اثر میگدارند، پس از ظاهر کردن فیلمها یک مفسر آنها را تفسیر میکند، باید در نظر داشت که زمان پرتودهی کوتاه باشد علاوه بر این، هر دو پرتو X و گاما برای سلامتی انسان مضر هستند.
اساس پرتونگاری بر این مبناست که در اثر پرتودهی دو پدیده عبور و جذب اتفاق بیافتد، در قسمتهایی از قطعه که ضخامت و یا چگالی زیاد است جذب پرتوها بیشتر شده و پرتوهای کمتری عبور میکنند در نتیجه تاثیر برروی فیلم کمتر است و این نواحی برروی فیلم روشنتر دیده میشود بصورت برعکس اگر در قطعه قسمتهای نازک یا قسمتهایی با چگالی کمتر و یا حفره وجود داشته باشد پرتوهای عبور یافته بیشتر میشود و بر روی فیلم بیشتر اثر میگذارد و آن قسمتهای فیلم تیرهتر دیده میشود، در پرتونگاری اغلب فیلمهای ظاهر شده میتوانند به عنوان یک مدرک یا یک سند دائمی باقیبمانند.
- تست فراصوتUltrasonic Testing:
در این تست از امواج فراصوتی که امواجی با فرکانس بالا هستند به منظور تعیین اندازه و موقعیت ناپیوستگیها و عیبها استفاده میشود، امواج فراصوت دارای فرکانس بین 25 تا 100000 مگاهرتز میباشند، این امواج توسط یک ترنسدیوسر مجهز به قطعه پیزوالکتریک تولید میشوند، در بازرسی با امواج اولتراسونیک این امواج به درون قطعه مورد آزمایش وارد میشوند، امواج وارد شده از سطح عیبها انعکاس یا اکو پیدا میکنند بنابراین عیوب قابل شناسایی هستند.
روشهای مختلفی از این آزمون وجود دارد که دو دسته اصلی آنها شامل:
1) روش دو ترنسدیوسری (یکی فرستنده و دیگری گیرنده): در این روش هرجا که عیب وجود داشته باشد شدت موج فراصوت کاهش یافته و در برخی موارد صفر میشود (چون موج صوتی در هوا منتشر نمیشود) پس عیب به راحتی شناسایی میشود.
2) روش تک ترنسدیوسری (پالس اکو): در این روش بر روی صفحه نمایشگر اغلب یک پالس اولیه و یک اکو از سطح پشت مشاهده میشود، در صورتی که درون قطعه عیب وجود داشته باشد یک اکو برای عیب نیز مشاهده میشود که به راحتی میتوان عیب راشناسایی کرد.
- تست جریان گردابیEddy Current Test:
در این روش از جریانهای گردابی که درون قطعات رسانا ایجائ میشود به منظور بازرسی عیبهای سطحی و زیرسطحی استفاده میشود، در این روش یک جریان الکتریکی متناوب از یک سیمپیچ عبور میکند و در نتیجه یک میدان مغناطیسی متناوب تشکیل میدهد در صورتی که قطعه رسانا به این سیمپیچ نزدیک شود، القای میدان مغناطیسی درون قطعه موجب میشود که جریان گردابی درون قطعه بوجود آید، جریان متناوب موجود در سیمپیچ باعث تغییر در میدان مغناطیسی میگردد، میدان مغناطیسی بر قطعه کار اثر می گذارد و باعث تولید جریان گردابی متغیر در آن میشود این جریانهای گردابی را میتوان با استفاده از یک سیمپیچ دریافت کرد و با اندازهگیری تغییرات جریان در سیم پیچ تحریک اولیه مقایسه کرد تغییرات در رسانای الکتریکی و یا نفوذپذیری مغناطیسی قطعه کار و یا حضور هر نوع عیبی باعث تغییر در جریان گردابی و در نتیجه تغییر در فاز و دامنه جریان اندازهگیری شده میشود.
ارسال نظر